At our sodium hypochlorite generator factory, we take pride in delivering high-quality disinfection systems worldwide. This time, we followed a shipment to Zambia—from production to installation. Here’s the full story.
Step 1: Order Confirmation and Production
The process began when our Zambian client placed an order. We confirmed specifications, including capacity, voltage, and materials. Our team then started manufacturing.
First, engineers prepared the generator frame. They used corrosion-resistant materials for durability. Next, they installed electrolytic cells, pumps, and control panels. Each component underwent strict quality checks.
After assembly, technicians tested the system. They ran simulated operations to ensure performance. Once approved, the generator was ready for packing.
Step 2: Secure Packaging
Proper packaging is crucial for safe transit. Our team followed international standards.
First, they wrapped the generator in waterproof film. Then, they placed it in a wooden crate with foam padding. This prevented movement during shipping. They also added desiccants to control moisture.
Finally, they labeled the crate clearly. The labels included handling instructions, weight, and destination details.
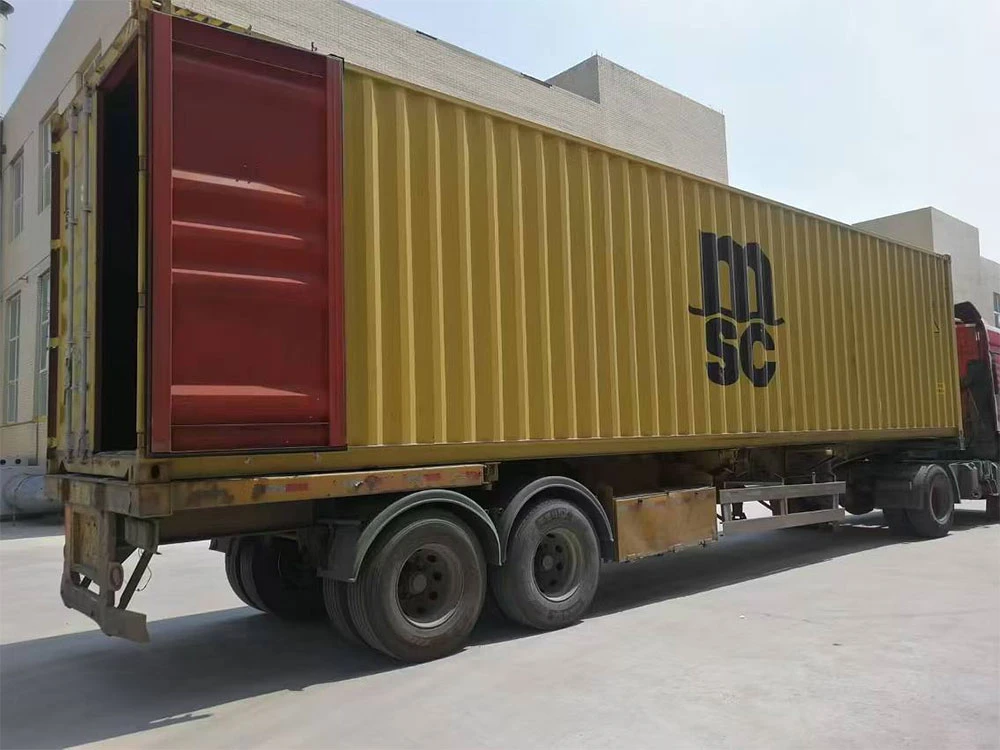
Step 3: Shipping Logistics
We coordinated with a reliable freight forwarder. The generator traveled by sea to Zambia.
First, the crate moved by truck to the nearest port. There, it was loaded into a container. The shipping documents—including the bill of lading and customs forms—were also prepared carefully.
The journey took several weeks. Our logistics team tracked the shipment daily. They updated the client regularly.
Step 4: Arrival in Zambia
When the shipment reached Zambia, customs clearance began. Our team provided all necessary documents in advance. This sped up the process.
After clearance, the generator was transported to the client’s site. We arranged a local logistics partner for safe delivery.
Step 5: On-Site Installation
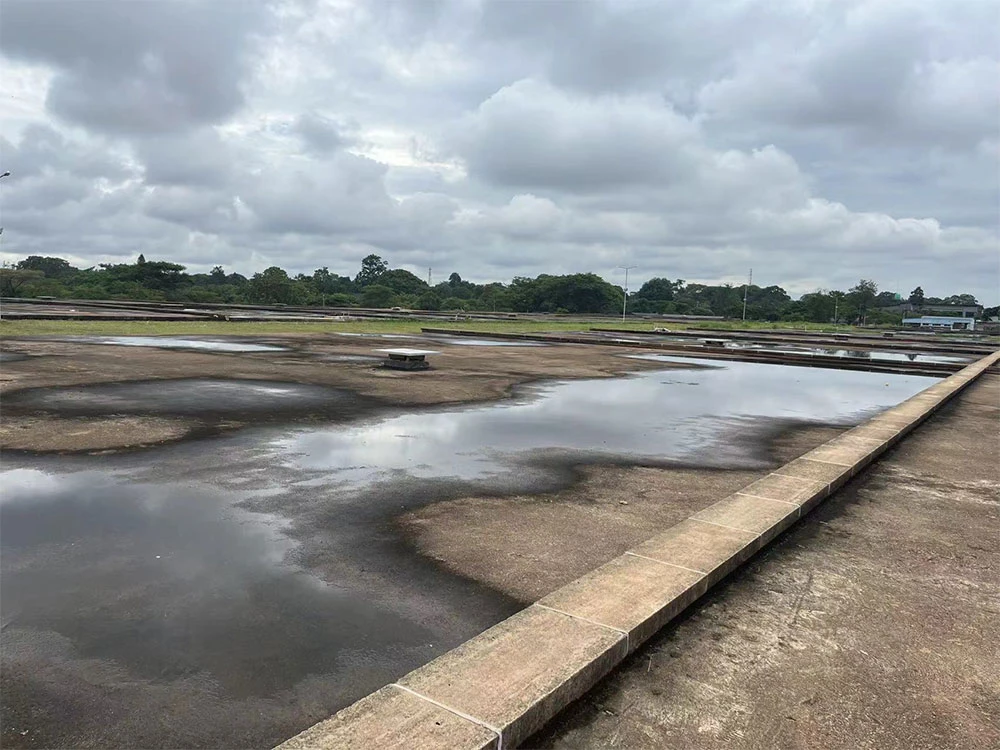
Our engineer flew to Zambia for installation. Meanwhile, the client prepared the site beforehand. They ensured proper space, power, and water supply.
First, the engineer uncrated the generator. He inspected it for any transit damage. Luckily, everything was intact.
Next, he positioned the system according to the layout plan. He connected the water inlet, power supply, and brine tank. Then, he calibrated the control panel.
Finally, he conducted a test run. The generator produced sodium hypochlorite solution successfully. The client’s team observed closely.
Step 6: Training and Handover
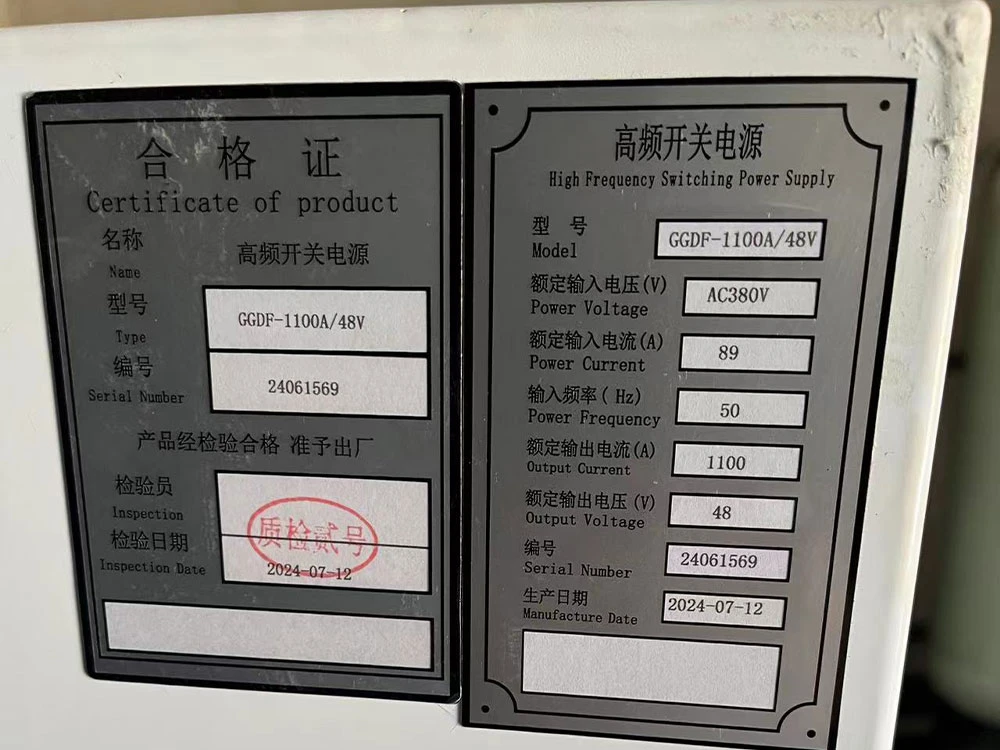
Our engineer trained the client’s staff. He explained daily operation, maintenance, and troubleshooting.
He also provided a detailed manual. The client practiced under supervision until confident.
After training, we handed over the system officially. The client signed the acceptance certificate.
Step 7: After-Sales Support
Our job didn’t end at installation. We offered remote support for any questions. We also scheduled follow-ups to ensure smooth operation.
From factory to Zambia, every step was carefully managed. Our team ensured quality, safety, and efficiency. The client was thrilled with the results.
At our factory, we don’t just sell sodium hypochlorite generators—we deliver complete solutions. Whether in Zambia or anywhere else, we make sure our systems work flawlessly.