1. Introduction
We’re excited to share another success story! Our hypochlorous acid (HOCl) generator has been successfully delivered to a food processing customer in Dandong. At the same time, the machine is now operating flawlessly, ensuring safe and efficient disinfection for food preservation.
This project also highlights our commitment to quality, from pre-delivery testing to on-site video guidance. Here’s how we made it happen.
2. Pre-Shipment Debugging: Ensuring Perfect Performance
Before shipping, every HOCl generator undergoes strict quality checks. For the Dandong customer, we took extra steps:
Functional Testing: We ran the machine for 48+ hours to verify stability.
Concentration Calibration: Adjusted the output to meet food-grade disinfection standards (50-200 ppm).
Leak & Pressure Checks: Confirmed no leaks and stable water/electrolyte flow.
Final Run Simulation: Also tested under conditions matching the customer’s usage (high humidity, continuous operation).
Why does this matter?
Pre-shipment debugging prevents on-site failures. The customer also receives a plug-and-play solution.
.
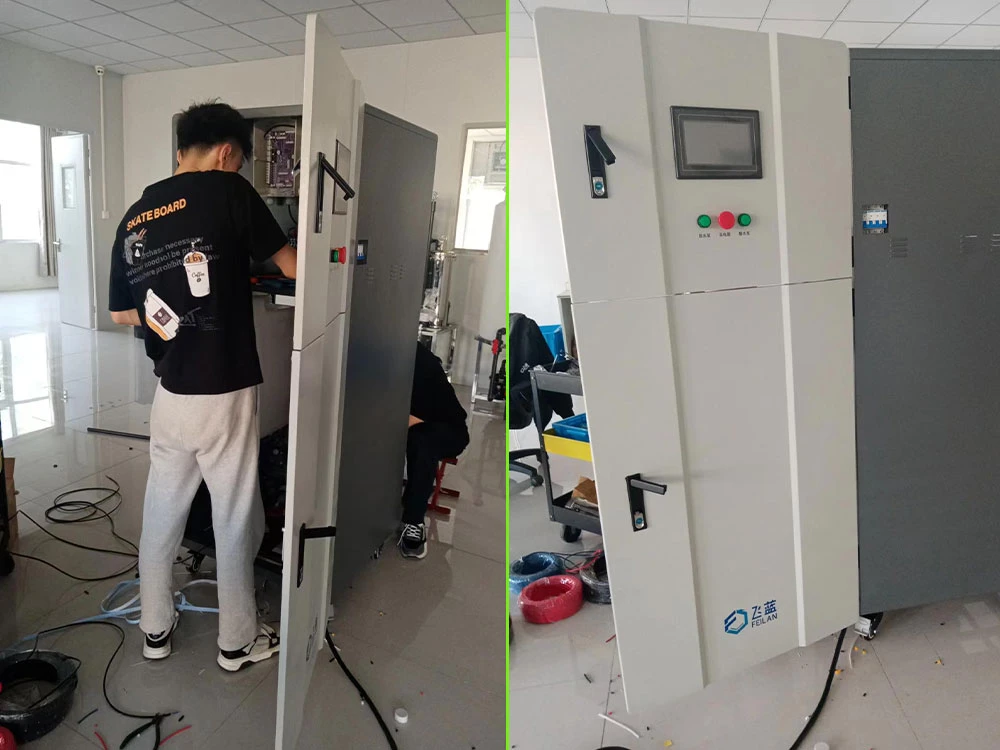
3. Smooth Delivery & Unboxing
The generator arrived in Dandong within 5 days (door-to-door logistics). We provided:
Detailed Unboxing Guide: Tools, parts list, and safety instructions.
Pre-Installation Checklist: Confirming power supply, water source, and workspace readiness at the same time.
The customer reported zero shipping damage – thanks to our shock-proof packaging!

4. Video Guidance for Hassle-Free Installation
Since our team couldn’t visit in person, we used real-time video calls to guide the installation:
Step 1: Setup
Position the unit near a water source and drain.
Connect inlet/outlet hoses (color-coded for easy identification).
Step 2: Power & Activation
Verify voltage (220V) and ground the system.
Fill the salt tank and start the electrolyte flow.
Step 3: First Run
Adjust chlorine concentration via the control panel.
Test output water with provided reagent strips.
Pro Tip: We recorded the session so the customer could rewatch key steps.
5. Customer Training & Troubleshooting
To ensure long-term success, we provided:
A 30-Minute Training Session: Covering daily operation, maintenance, and safety.
FAQ Document: Addressing common issues (e.g., “Low output? Check salt purity!”).
Remote Monitoring: We can also diagnose problems via the machine’s data logs.
The customer mastered the system quickly – no surprises!
6. Successful Application in Food Disinfection
Now, the HOCl generator is also running 24/7 for:
Surface Sanitization: Conveyor belts, tools, and packaging.
Ingredient Rinsing: Extending shelf life of vegetables and seafood at the same time.
Air Disinfection: Nebulized HOCl in storage rooms.
Key Benefits Noticed by the Customer:
1. No chemical residues (unlike traditional disinfectants).
2. 99.9% pathogen kill rate (lab-tested).
3. Lower costs compared to chlorine tablets.

7. Why Choose Our HOCl Generators?
Plug-and-Play Design: Minimal setup, maximum efficiency.
24/7 Support: Even post-installation, we’re just a call away.
Food-Safe Compliance: Meets USDA, FDA, and EU standards.
Conclusion
Another happy customer in Dandong! From rigorous pre-shipment tests to remote installation support, we also ensure every HOCl generator works perfectly from Day 1.
Interested? Meanwhile, contact us today for a free consultation! Let’s upgrade your food safety process with HOCl technology.
Need more details? I can add:
Technical parameters (flow rate, power consumption).
Comparison with competitors.
Customer interview quotes.